Glossario tecnico
Contattaci
Lo stampo è un’attrezzatura, composta da numerosi componenti diversi sia per materiale che per geometria, che deve riprodurre un pezzo in specifica.
Le principali caratteristiche di questa tipologia di stampi sono la necessità di resistere a temperature molto elevate, sollecitazioni meccaniche, chimico e fisiche.
Lo stampo tradizionale è costituito da due semi-parti: una parte fissa e una parte mobile.
Uno stampo per pressofusione è solitamente composto da varie parti ognuna delle quali con caratteristiche e funzioni specifiche, ricordiamo di seguito alcuni dei componenti principali:
- Matrici: Divise solitamente in due parti (mobile e fissa) sono il negativo della forma da produrre (il pezzo). Le matrici vengono realizzate tramite lavorazioni meccaniche con asportazione di truciolo o elettroerosione, al fine di ottenere la forma geometrica del componente. Sono altresì presenti una serie di forature che realizzano i circuiti di termoregolazione. Le matrici vengono quindi trattate termicamente al fine di ottenere il giusto grado di durezza e resistenza all’usura a caldo.
- Inserti stampanti: Vi sono situazioni in cui, l’usura eccessiva, dovuta alla geometria del pezzo e dalle condizioni stesse di utilizzo dell’attrezzatura, creano delle aree delimitate nella matrice, che comportano la necessità di realizzare particolari che vengono inseriti nelle matrici stesse. Questi inserti devono essere di facile sostituzione e manutenzione, possiedono generalmente una vita utile inferiore alla matrice e necessitano di essere cambiati con frequenze maggiori.
- Movimenti: Alcune geometrie di pezzo possono presentare zone che non lo rendono stampabile se non con l’aggiunta di movimentazioni oltre che all’apertura dei piani pressa. Questi movimenti sono atti a liberare i cosiddetti «sottosquadri» presenti nel pezzo da produrre. Tali movimenti possono essere principalmente di tre tipologie: meccanico, idraulico o misto.
- Portastampi: Solitamente diviso in due parti (mobile e fissa), il portastampo ha la funzione di contenere le matrici. Devono essere costruiti in modo da permettere la manutenzione più comoda possibile della componentistica montata al loro interno e garantire la solidità strutturale a lungo termine per la produzione di massa.
- Castello: Ha la funzione principale di contenere le piastre che permettono l’estrazione del pezzo, oltre allo staffaggio dello stampo alla pressa di produzione e il sostegno al portastampo mobile.
- Tavolini di estrazione: Hanno la funzione di muovere gli espulsori per separare il pezzo prodotto dallo stampo; possono talvolta muovere dei settori “cuspidi” per risolvere dei sottosquadri di entità limitata in figura.
Il processo di pressocolata di leghe metalliche a camera calda, anche detto “iniettofusione”, è caratterizzato da un forno fusorio integrato nella macchina di pressocolata e da un dispositivo di iniezione immerso nel crogiolo. Tale metodologia consente di ottenere tempi ciclo ridotti, maggior controllo delle temperature e meno rischi di ossidazione della lega ma, a causa della sua conformazione, è attuabile solamente con leghe basso fondenti. Risulta, dunque, idonea per leghe caratterizzate da una temperatura di fusione inferiore a 450°C, come le leghe di zinco e di piombo, mentre può essere utilizzata solo in condizioni particolari per le leghe di alluminio e di magnesio che vanno ad usurare eccessivamente il dispositivo di iniezione.
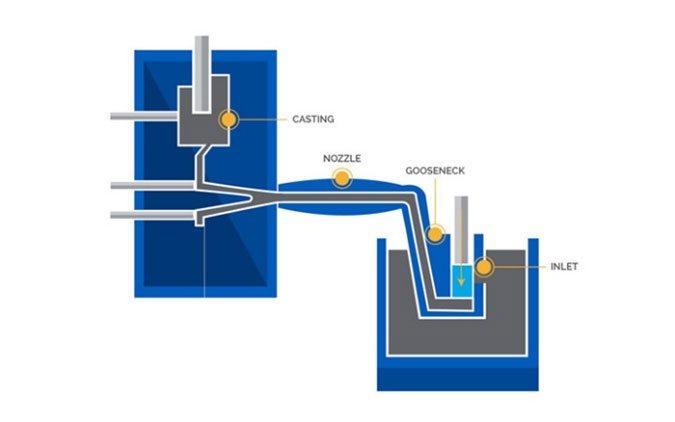
Esistono due tipologie principali di pressocolata a camera calda:
- A PISTONE TUFFANTE (più diffusa): Il materiale entra all’interno del dispositivo di iniezione tramite una zona di passaggio e viene iniettato grazie al movimento verticale del pistone che spinge la lega lungo i canali fino al riempimento della/e cavità dello stampo.
- A CAMERA DI PRESSIONE OSCILLANTE (meno diffusa): la camera si riempie basculando mentre il getto viene estratto e, una volta richiuso lo stampo, torna nella sua posizione consentendo l’iniezione tramite l’azione dell’aria compressa sulla superficie del metallo liquido.
Il processo di pressocolata di leghe metalliche a camera fredda, anche detto “pressofusione”, è caratterizzato da un dispositivo di iniezione completamente indipendente dal forno fusorio. Tale metodologia consente di ridurre i costi di mantenimento e, soprattutto, di ottenere velocità e pressioni di iniezione maggiori, oltre ad essere fondamentale per alcune leghe alto-fondenti come l’alluminio e il magnesio.
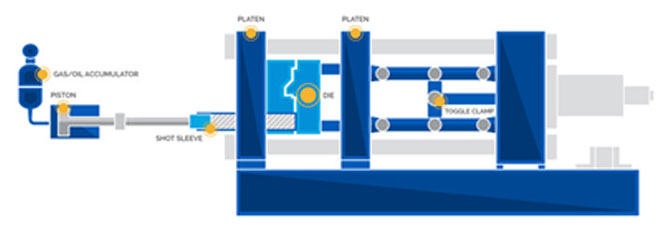
La lega metallica, dopo esser stata versata all’interno del cilindro di iniezione, viene spinta nella cavità attraverso l’ugello tramite l’azione di un cilindro seguendo tre fasi:
- 1^ FASE (Pre-riempimento): velocità e pressioni modeste per ridurre al minimo l’inglobamento d’aria fino al raggiungimento degli attacchi di colata.
- 2^ FASE (Riempimento): aumento delle velocità e delle pressioni fino al riempimento completo della cavità.
- 3^ FASE (Post-pressione): ulteriore aumento della pressione e annullamento della velocità per compensare il ritiro di solidificazione.
Il processo di Thixomoulding da granulato di magnesio consiste nell’inserimento di granuli di magnesio all’interno di una tramoggia fino al raggiungimento della saturazione volumetrica in presenza di argon. In fase di iniezione, il granulato attraversa una zona caratterizzata dalla presenza di una vite che, sottoponendo il materiale ad uno sforzo di taglio, frantuma le dendriti presenti nella fase liquida (il prefisso “Thixo” indica la presenza di una frazione solida maggiore o uguale al 50%) generando particelle sferoidali in stato semisolido thixotropico, ovvero in grado di diventare liquide tramite l’agitazione meccanica che viene effettuata mediante iniezione all’interno della cavità stampo.
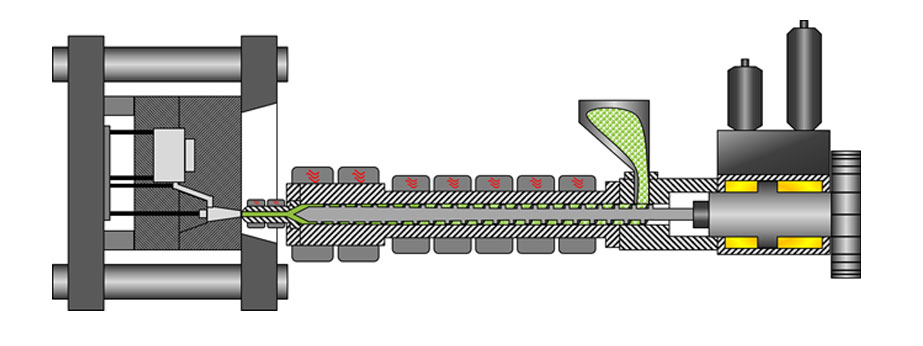
I vantaggi principali di questa tipologia di processo sono legati alla struttura equiassica dei getti ottenuti, oltre alla ripetibilità, alla complessità e al controllo delle parti prodotte, consentendo la realizzazione di getti “near-net-shape” (vicino alla forma richiesta da progetto). Inoltre, risulta particolarmente idonea per le leghe di magnesio in quanto consente di non portarle allo stato fuso, evitando i rischi del contatto di quest’ultimo con l’aria.
Il processo di stampaggio ad iniezione è un processo produttivo utilizzato a livello industriale per la produzione di manufatti in materiale polimerico termoplastico. In particolare, il materiale viene portato ad una temperatura tale per cui risulta plastificato e può essere iniettato nella cavità stampo mediante l’applicazione di una pressione elevata.
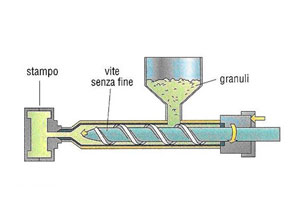
Lo schema di funzionamento del processo, come sintetizzato nell’immagine, è caratterizzato da una tramoggia dove viene inserito il materiale sotto forma di granuli. Il componente fondamentale dello stampaggio è la vite senza fine che presenta due movimenti principali:
- Rotazione intorno al suo asse: tale movimento, insieme all’energia termica fornita da un ampio numero di resistenze collocate lungo il cilindro, consente la plastificazione del polimero;
- Avanzamento: consente l’iniezione del fuso polimerico nella cavità stampo per la realizzazione del manufatto.
L’ultimo componente fondamentale è lo stampo che dà la forma al polimero e da cui il pezzo viene estratto una volta che il materiale risulta solidificato e sufficientemente raffreddato.
Iniezione termoplastica monomateriale
L’iniezione termoplastica monomateriale è realizzata mediante il processo di stampaggio sopra descritto ed è caratterizzata dall’utilizzo di un singolo tipo di polimero per l’ottenimento del pezzo finale. È la tipologia più semplice di stampaggio realizzabile e presenta tempi ciclo ridotti rispetto alle altre non essendo interessata da iniezioni di polimeri differenti, gas e altre caratteristiche che influenzano sia la complessità che la durata dei processi. D’altro canto, però, risulta difficile il raggiungimento di performance estetiche e strutturali idonee per alcune tipologie di pezzi. Infatti, soprattutto con l’utilizzo di polimeri quali le “commodities” (in particolare PE e PP), le prestazioni meccaniche dei pezzi ottenuti sono modeste e possono presentarsi problematiche quali risucchi e ritiri che compromettono l’aspetto dei manufatti e vanno ulteriormente a limitare il campo di applicazione meccanico, soprattutto in settori quali automotive e aerospace. Con l’utilizzo di tecnopolimeri o materiali polimerici caricati con additivi, tuttavia, è possibile migliorare le performance in esercizio, anche se la progettazione e la scelta della carica corretta rivestono un ruolo fondamentale.
INIEZIONE TERMOPLASTICA MULTIMATERIALE
L’iniezione termoplastica multimateriale, contrariamente alla monomateriale, è una tipologia di iniezione caratterizzata dall’utilizzo di più materiali differenti sia dal punto di vista delle proprietà meccaniche che di quelle chimico-fisiche. Rispetto allo stampaggio monomateriale, la complessità e la durata del processo sono sicuramente più elevate e richiede un’ottimizzazione specifica delle tempistiche di stampaggio di uno o l’altro ugello necessitando, talvolta, di soluzioni complesse sia per la macchina che per lo stampo. Esistono varie possibilità in questo campo:
Stampaggio bimateriale 2K: lo stampaggio è caratterizzato dalla presenza di due materiali differenti e consente l’ottenimento di pezzi con elevate caratteristiche estetiche, di tenuta e di performance. Tali proprietà rappresentano un requisito necessario in applicazioni strutturali come nel campo automotive. L’unione dei due materiali viene raggiunta mediante la temperatura e lo studio della chimica molecolare dei differenti polimeri impiegati, consentendo di resistere sia a temperature e pressioni elevate, sia agli agenti atmosferici o ambientali che si possono riscontrare in esercizio.
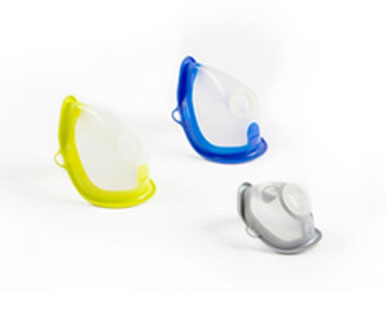
Stampaggio trimateriale 3K: lo stampaggio è caratterizzato dalla presenza di tre materiali differenti, consentendo l’ottenimento di pezzi estremamente tecnici o con particolari requisiti dal punto di vista estetico. Un’altra applicazione importante è la realizzazione di manufatti con colori differenti all’interno.
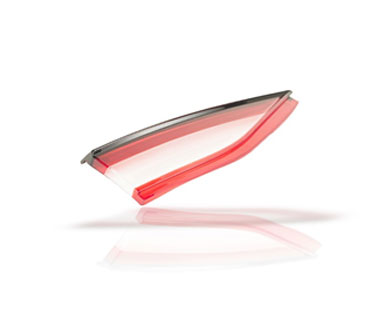
INIEZIONE COSTAMPATI (INSERT MOULDING)
L’insert moulding, o co-stampaggio ad iniezione, è una tipologia di processo di stampaggio caratterizzato dall’iniezione di materiale polimerico in una cavità stampo dove sono già stati posizionati degli inserti o dei substrati necessari per l’ottenimento del pezzo finale. Lo scopo principale di questa tecnica, oltre alla possibilità di realizzare pezzi difficilmente ottenibili in altro modo, è ridurre notevolmente le operazioni successive alla fase di stampaggio, come quelle di finitura e di montaggio, consentendo una riduzione dei tempi ciclo totali e automatizzando il processo. Le tipologie di inserti possono essere differenti o realizzate in materiali diversi (altre tipologie di polimeri, metalli, materiali ceramici, ecc) e, solitamente, presentano delle superfici pre-lavorate che facilitano l’adesione del materiale in fase di stampaggio: un esempio classico è rappresentato dagli inserti filettati in materiale metallico.
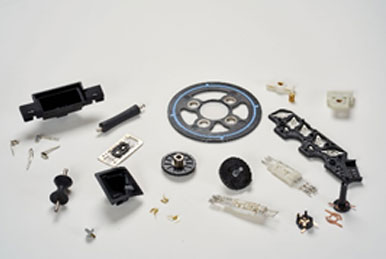
INIEZIONE ASSISTITA DA GAS (GIM)
Lo stampaggio ad iniezione assistito da gas, detto GIM o GAIM, è una tipologia di stampaggio ad iniezione caratterizzata, nelle fasi finali, dall’utilizzo di un gas in pressione che spinge il materiale contro le pareti o all’estremità dello stampo. La metodologia di base è la medesima del classico stampaggio ad iniezione ma, quando il materiale ha riempito l’80% circa della cavità, tramite una serie di canali di ingresso appositamente studiati, viene insufflato del gas che svolge le funzioni citate in precedenza. Mediante questa tecnica è possibile ridurre sia il peso che il costo dei pezzi realizzati, ottenendo pezzi cavi con spessori più elevati, meno deformazioni e meno risucchi superficiali. Vi sono, però, anche delle controindicazioni, soprattutto per gli stampi multi-cavità: infatti, non è facile la realizzazione di canali e impianti idonei per il gas quando vi sono impronte differenti tra loro.
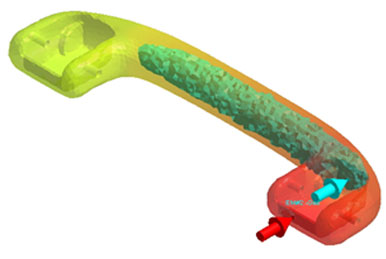
INIEZIONE MuCell CON ESPANSIONE MICROCELLULARE
Lo stampaggio ad iniezione tramite tecnica MuCell con espansione microcellulare è una tecnica relativamente moderna ma già ampiamente utilizzata per la realizzazione di pezzi in materiale polimerico. Gli aspetti innovativi di questa tecnica derivano dalla miscelazione di polimero e gas inerte direttamente nel cilindro di iniezione. Una volta che la miscela ha raggiunto la cavità stampo, con la riduzione di pressione, il gas tende ad espandere andando a ridurre il peso, essendo la densità del gas inferiore a quella del polimero, e le deformazioni, presentando un ritiro uniforme e controllato su tutto il pezzo: infatti, con i processi tradizionali di stampaggio il controllo del raffreddamento è attuato mediante il mantenimento applicato dalla pressa, ma le variazioni nella lunghezza di flusso possono creare disomogeneità, provocando deformazioni, risucchi e altre difettologie caratteristiche mentre, con questa tecnologia, tali problemi sono notevolmente ridotti.
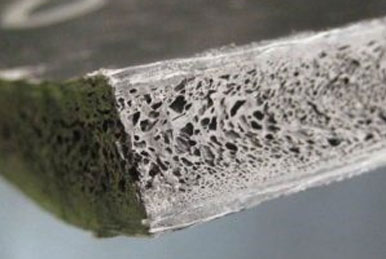
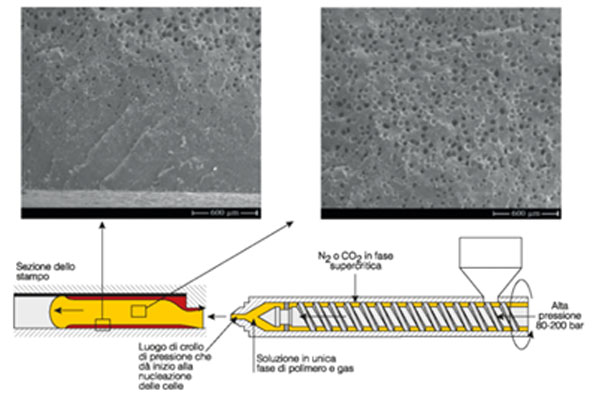
Tempra sottovuoto
Il trattamento termico di tempra degli acciai è svolto riscaldando il materiale al di sopra della temperatura di austenitizzazione e, successivamente, raffreddandolo bruscamente, tramite l’utilizzo di mezzi tempranti, per ottenere una struttura martensitica. La martensite presenta un’elevata durezza e un carico di rottura notevole, ma una resilienza bassa che la rende estremamente fragile. Per questo motivo, a seguito del trattamento di tempra, vengono svolti uno o più trattamenti di rinvenimento riscaldando il materiale al di sotto del punto Ac1 ed evitando, in questo modo, che risulti eccessivamente fragile generando cricche e rotture nello stampo. L’insieme dei trattamenti di tempra e rinvenimento prende il nome di bonifica.
In particolare, la tempra sottovuoto (pari a circa 10-3 bar) è ottenuta riscaldando il materiale in un range di temperature tra 800 e 1200°C sulla base del contenuto di carbonio e introducendo azoto ad una pressione tra i 2 e 12 bar. Questo trattamento consente di ottenere strutture martensitiche isotrope con valori resistenziali elevati e deformazioni contenute, anche se generalmente è seguito, comunque, da una o più fasi di rinvenimento.
Lo studio delle curve di raffreddamento caratteristiche del materiale, delle composizioni chimiche e degli spessori delle parti coinvolte è fondamentale per ottenere un componente temprato correttamente fino a cuore, evitando in questo modo problematiche resistenziali e deformazioni eterogenee tra zone diverse.

Nitrurazione gassosa
Il trattamento termochimico di nitrurazione degli acciai è un processo industriale di indurimento superficiale svolto ad una temperatura di circa 520-540°C che si realizza tramite la formazione di nitruri. In particolare, la nitrurazione gassosa si basa sulla reazione di dissociazione dell’ammoniaca che è catalizzata dall’acciaio:

Tale reazione produce azoto atomico che riesce a penetrare all’interno della struttura cristallina superficiale dell’acciaio superando il limite di solubilità e provocando indurimento tramite la formazione di nitruri.
A seguito del trattamento di nitrurazione, si formano zone differenti all’interno dell’acciaio:
- Coltre bianca: zona superficiale formata da nitruri che consente la diffusione di azoto nella matrice metallica. È solitamente molto fragile e può essere asportata mediante un processo di rettifica;
- Zona di diffusione: zona caratterizzata dalla diffusione dell’azoto e maggiormente interessata dall’indurimento;
- Zona di transizione: zona solo limitatamente interessata dalla diffusione che rappresenta il passaggio tra la zona di diffusione e il materiale base.
La nitrurazione, oltre ad indurire l’acciaio, aumenta anche la resistenza ad usura, a fatica e alla corrosione (soprattutto con un trattamento ulteriore di post-ossidazione). Inoltre, è un trattamento che, a seconda delle tempistiche e dei parametri impostati per il forno, può penetrare in modo differente all’interno dell’acciaio. Infatti, componenti classici che vengono sottoposti ad una nitrurazione superficiale sono le parti stampanti e i tasselli, mentre sono sottoposti a trattamenti di nitrurazione profonda i componenti di scorrimento quali le guide.
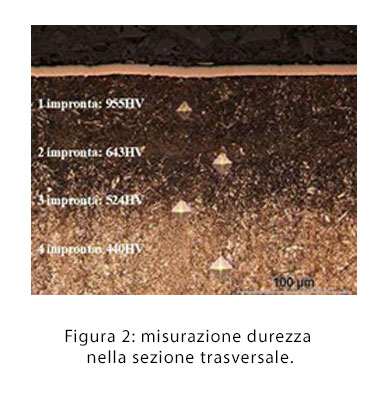
Carbo-nitrurazione
Il trattamento termochimico di carbo-nitrurazione è un processo metallurgico caratterizzato dalla diffusione di carbonio e azoto all’interno dell’acciaio. È un trattamento simile alla cementazione, anche se viene svolto a temperature inferiori (tra 720 e 910°C) e presenta meno deformazioni, ma è caratterizzato dalla presenza di ammoniaca con diffusione di azoto che porta alla formazione di uno strato superficiale notevolmente indurito. Per un trattamento efficace, solitamente, è preceduta da una fase di distensione volta ad eliminare le tensioni residue. Il vantaggio principale di questa tipologia di trattamento è l’aumento della resistenza ad usura, soprattutto a secco, del materiale e per questo motivo è applicata ad alberi, ingranaggi e pistoni. Talvolta, successivamente alla carbo-nitrurazione, viene svolta una fase di rinvenimento per ridurre al minimo la fragilità dell’acciaio, evitando cricche e rotture.
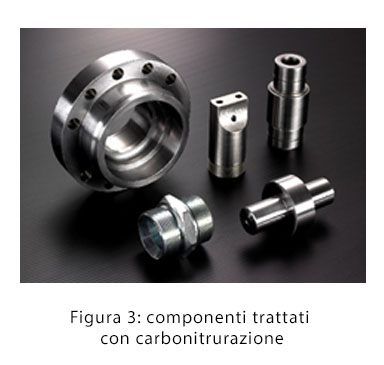
Invecchiamento
Il trattamento termico di invecchiamento è definito anche “indurimento per precipitazione” ed è un trattamento solitamente svolto successivamente alla tempra o alla solubilizzazione. Infatti, tramite queste fasi, che sono caratterizzate da un brusco raffreddamento, viene indotto il congelamento della struttura e inibita la diffusione degli elementi chimici. Al termine del raffreddamento si instaura un meccanismo di invecchiamento naturale, a temperatura ambiente, ma è anche possibile riscaldare il materiale inducendo un invecchiamento artificiale che porta alla nucleazione e coalescenza delle particelle (che possono essere sia coerenti che incoerenti a seconda della fase). Tali aggregati vanno a costituire degli ostacoli al movimento delle dislocazioni, richiedendo sforzi maggiori per instaurare delle deformazioni e, quindi, indurendo il materiale: infatti, le dislocazioni, per superare queste particelle, devono spendere energia secondo il meccanismo di taglio o quello di Orowan.
Un aspetto importante di questo trattamento è il controllo dell’accoppiamento tempo-temperatura: tempi di riscaldamento troppo lunghi, infatti, non portano benefici al materiale ma si entra nella fase di “sovra invecchiamento” con dimensioni delle particelle eccessive e riduzione della durezza rispetto al valore ottimale.
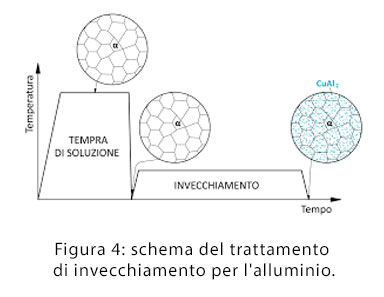
Ossidazione
Il trattamento chimico di ossidazione è volto alla protezione superficiale del materiale metallico tramite deposizione di uno strato di ossido che funge da strato protettivo, prevenendo l’attacco da parte degli agenti atmosferici che può indurre stress o fenomeni corrosivi. Inoltre, lo strato superficiale che si forma può fungere, successivamente, da substrato per l’applicazione di vernici o altri rivestimenti. Le varie tipologie di ossidazione si distinguono per il colore superficiale, lo spessore (in parte si forma superficialmente e in parte penetra nell’acciaio), e altre caratteristiche chimiche e fisiche.
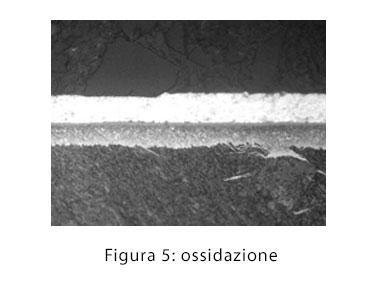
Distensione
Il trattamento termico di distensione viene svolto scaldando l’acciaio ad una temperatura inferiore ad Ac1 e, successivamente, raffreddandolo lentamente fino a temperatura ambiente. Lo scopo di questo trattamento è andare ad eliminare le tensioni generate dalle fasi produttive precedenti senza alterare la durezza, prevenendo eventuali deformazioni che possono verificarsi nelle fasi successive. Inoltre, la scelta di effettuare il raffreddamento in forno o in aria in un periodo di tempo prolungato è fatta per evitare di indurre ulteriori tensioni nel materiale.
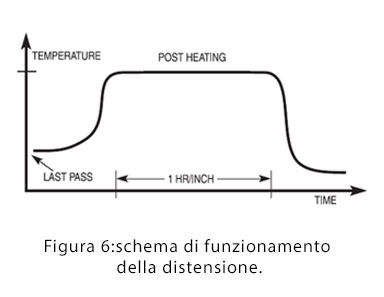
Distensione con post-ossidazione
Il trattamento termico di distensione descritto può essere ulteriormente completato tramite un trattamento chimico di post-ossidazione che va ad aumentare la resistenza a corrosione e favorisce il distacco dell’alluminio, in pressofusione, dall’acciaio dello stampo. La post ossidazione è una tipologia di trattamento che può essere effettuata anche al termine della nitrurazione tramite l’utilizzo di aria, protossido di azoto (N2O ) e anidride carbonica (CO2). I vantaggi principali riguardano:
- Resistenza a corrosione aumentata;
- Resistenza ad usura migliorata;
- Finitura superficiale ottima.
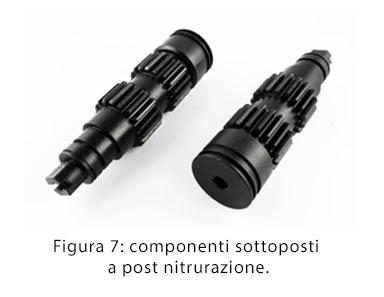